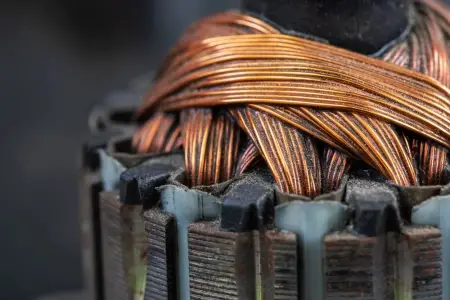
Um comutador é um componente essencial em motores elétricos de corrente contínua (CC) e alguns geradores elétricos. Sua principal função é atuar como retificador mecânico e interruptor rotativo, permitindo a reversão periódica da direção da corrente nos enrolamentos do rotor. Esse processo é conhecido como comutação.
O comutador é composto de segmentos de cobre eletrolítico duro, isolados uns dos outros por material dielétrico, como mica. Esses segmentos são montados no eixo do rotor e conectados aos enrolamentos da armadura. Para garantir a transmissão de corrente, o comutador interage com escovas de carvão, que permanecem em contato constante com sua superfície.
Como funciona o comutador de um motor elétrico?
O comutador consiste em um conjunto de barras de contato fixadas ao eixo rotativo do motor e conectadas aos enrolamentos da armadura. Seu funcionamento é baseado nos seguintes princípios:
- Quando o rotor gira, as escovas de carvão deslizam sobre os segmentos do comutador, permitindo que a corrente elétrica seja condutiva aos enrolamentos da armadura.
- À medida que o rotor completa meia revolução, a conexão do comutador com as escovas muda, invertendo a direção da corrente no enrolamento.
- Em um motor CC, essa reversão de corrente gera um campo magnético na armadura que interage com o campo fixo do estator, produzindo um torque constante que mantém o rotor girando em uma única direção.
- Em um gerador, o movimento mecânico do eixo gera uma corrente alternada nos enrolamentos da armadura, que é então retificada pelo comutador para obter corrente contínua no circuito externo.
- O número de segmentos no comutador influencia a suavidade da comutação: quanto mais segmentos houver, mais suave será a transição de corrente, reduzindo faíscas e desgaste das escovas.
- O projeto do comutador e das escovas deve garantir contato eficiente para minimizar a resistência de contato e a geração excessiva de calor, fatores que podem afetar a eficiência do motor.
- Um comutador bem projetado permite um desempenho estável do motor ao reduzir o ruído elétrico e otimizar a transferência de corrente entre as partes móveis e estacionárias do sistema.
- No setor automotivo, são utilizadas variantes especializadas, como o comutador automotivo e o comutador de carro , que permitem a comutação eficiente em sistemas de partida e acionamento de veículos elétricos. Um caso específico é o comutador de partida , usado em motores de partida de automóveis para garantir a ativação confiável do motor de combustão interna.
Tipos de comutadores
Existem vários tipos de comutador, projetados para atender a diferentes aplicações e requisitos operacionais. Os mais relevantes são descritos abaixo:
Comutador de tambor
Comum em motores de maior potência, esse tipo de comutador é composto por segmentos de cobre dispostos em formato cilíndrico ao redor do eixo do rotor. Seu design robusto permite lidar com altas correntes e é comum em motores industriais e sistemas de tração elétrica.
Troca de disco
Embora menos comum, esse tipo é caracterizado por ter segmentos planos organizados em um disco giratório. Ele é usado em aplicações específicas onde é necessário um design mais compacto e leve, como em certos dispositivos eletrônicos e pequenos motores.
Comutador multissegmento
Projetado para aplicações que exigem comutação mais suave e eficiente, esse tipo de comutador incorpora um número maior de segmentos, reduzindo a formação de faíscas e melhorando a estabilidade do motor. É usado em motores de precisão, ferramentas elétricas de alta velocidade e sistemas de controle avançados.
Desgaste e manutenção do comutador
Devido ao atrito contínuo com as escovas de carvão, o comutador está sujeito a desgaste ao longo do tempo. Alguns problemas comuns incluem:
- Desgaste irregular : pode causar faíscas excessivas e comutação incorreta.
- Sujeira e resíduos de carbono : o acúmulo na superfície do comutador pode afetar o contato elétrico.
- Desalinhamento das escovas : pode causar desgaste acelerado e perda de eficiência.
A manutenção do comutador inclui limpeza regular, inspeção do desgaste das escovas e, em alguns casos, retificação da superfície do comutador para restaurar a operação adequada.
Qual é a finalidade do comutador em um motor elétrico?
O comutador desempenha diversas funções fundamentais na operação de motores e geradores elétricos de corrente contínua:
- Conexão elétrica : Estabelece uma conexão entre as escovas estacionárias e os enrolamentos do rotor no eixo rotativo.
- Mudança de direção da corrente : Ao girar, inverte a polaridade da corrente nos enrolamentos do rotor no momento preciso, garantindo um torque constante na mesma direção.
- Sensor de posição angular : Seu design permite detectar a posição do rotor em relação ao campo magnético.
- Conversão de corrente : Em geradores de corrente contínua, transforma a corrente alternada induzida nos enrolamentos em uma corrente de saída contínua.
Em um alternador, a corrente alternada gerada pelo movimento do rotor através do campo magnético fixo é convertida em tensão de corrente contínua pelo comutador. Em um motor elétrico, a reversão periódica da corrente nos enrolamentos do rotor permite que a armadura continue girando continuamente.